Tier 1 suppliers are under pressure to move more parts faster and with greater precision than ever before. As automotive production becomes increasingly complex, intralogistics solutions must adapt to handle a wide range of components—from delicate electronics to heavy mechanical assemblies—in real time across multiple workshops.
ForwardX Robotics is addressing this challenge with one of the largest known deployments of autonomous mobile robots (AMRs) in the automotive sector: 435 AMRs are now in operation at Chery’s Dalian plant . They are transforming internal logistics and setting a new benchmark for scalable, intelligent automation in the industry.
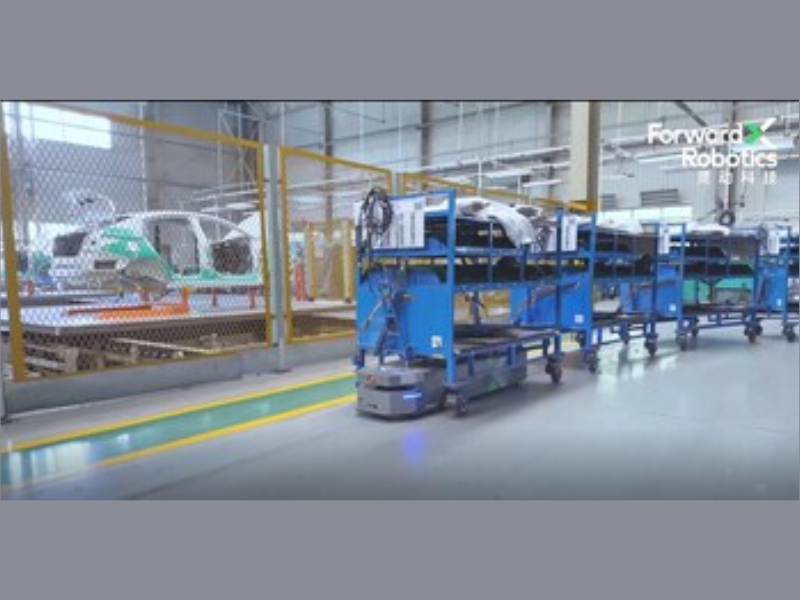
Tailored AMRs for complexity for Tier 1
The ForwardX solution includes three specialized AMR models that work together to optimize movements across the entire manufacturing floor to meet the evolving needs of Tier 1 suppliers:
- Flex Series AMRs: These maneuverable units are ideal for transporting small, delicate components such as printed circuit boards and wiring assemblies with just-in-time precision and minimal floor impact.
- Max Series AMRs : These high-performance robots move heavy objects such as motors and machine parts and integrate seamlessly into production lines to avoid delays.
- Lynx U1000 – Towing AMRs: This series is specifically designed for towing larger frames and bulky materials and is fully integrated with Chery’s PLC system to enable autonomous delivery in key production areas.
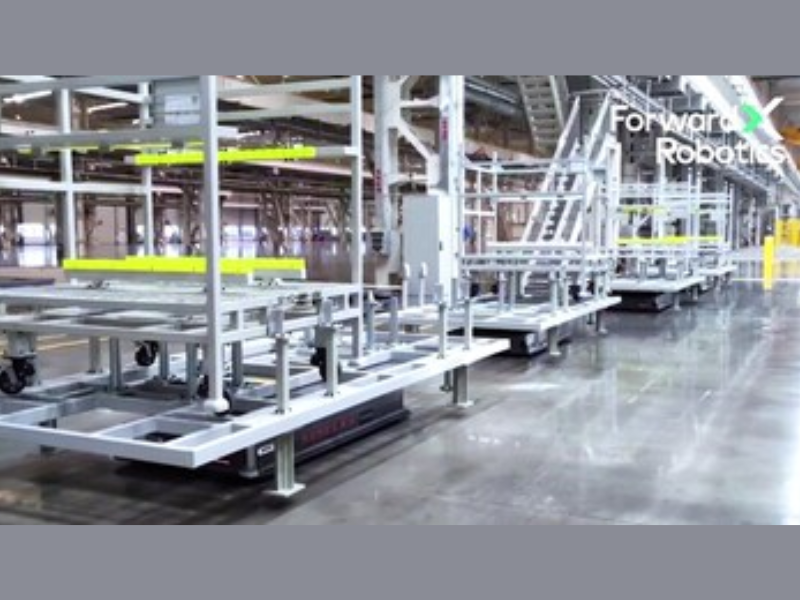
“This deployment reflects our commitment to solving real manufacturing problems at scale,” said Nicolas Chee , Managing Director of ForwardX Robotics. “Chery Automobile challenged us to streamline material flow in one of their most complex facilities—and with 435 AMRs working harmoniously together, we are creating a new era of intelligent intralogistics.”
Seamless automation across multiple workshops
The result? A synchronized flow of materials—both large and small parts—between stamping, welding, battery, and final assembly workshops, with minimal interruptions and maximum uptime. Chery’s factory can now deliver a vehicle every two minutes, supported by autonomous logistics that adapts in real time.
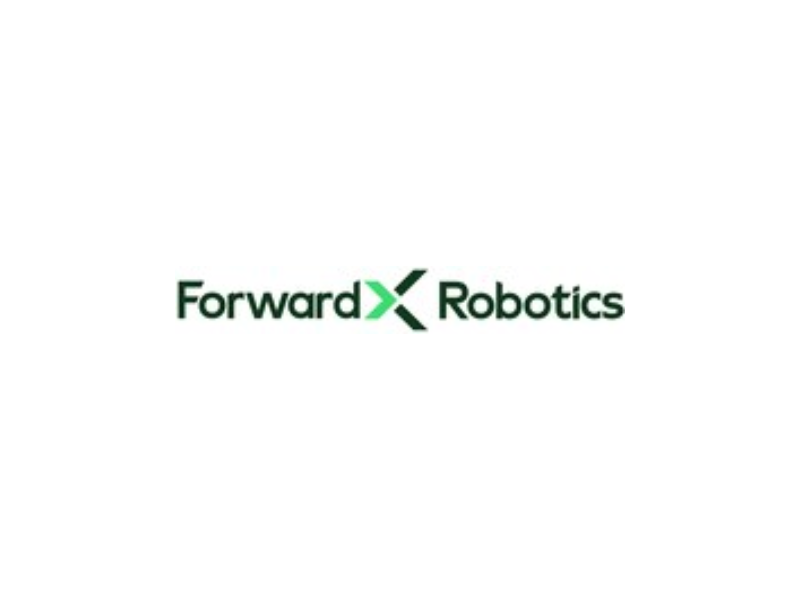
Proven throughout the automotive supply chain
ForwardX technology has already been successfully deployed by other leading manufacturers in Asia, highlighting its versatility in different workflows and factory environments:
- At Inalfa, the Max-1500L Series AMRs excel in workshops with confined roof systems, moving heavy loads with precision through narrow pathways.
- At BYD, customized forklifts with 2.4-meter forks automate material handling in the high-demand EV battery plants and navigate safely through hazardous areas.
- At Dongfeng Auto, Lynx U1000 AMRs transport car doors in the welding workshop, keeping pace with the high-speed production lines.
These projects demonstrate ForwardX’s strength in solving general and highly specialized intralogistics challenges – from transporting large frames to handling delicate components – all with flexible, scalable robotics that can be integrated into existing operations.
Read Similar News:
NVIDIA announces a major release of its Omniverse platform
Fast and furious: The Roadmap to Italy’s Automotive resurrection